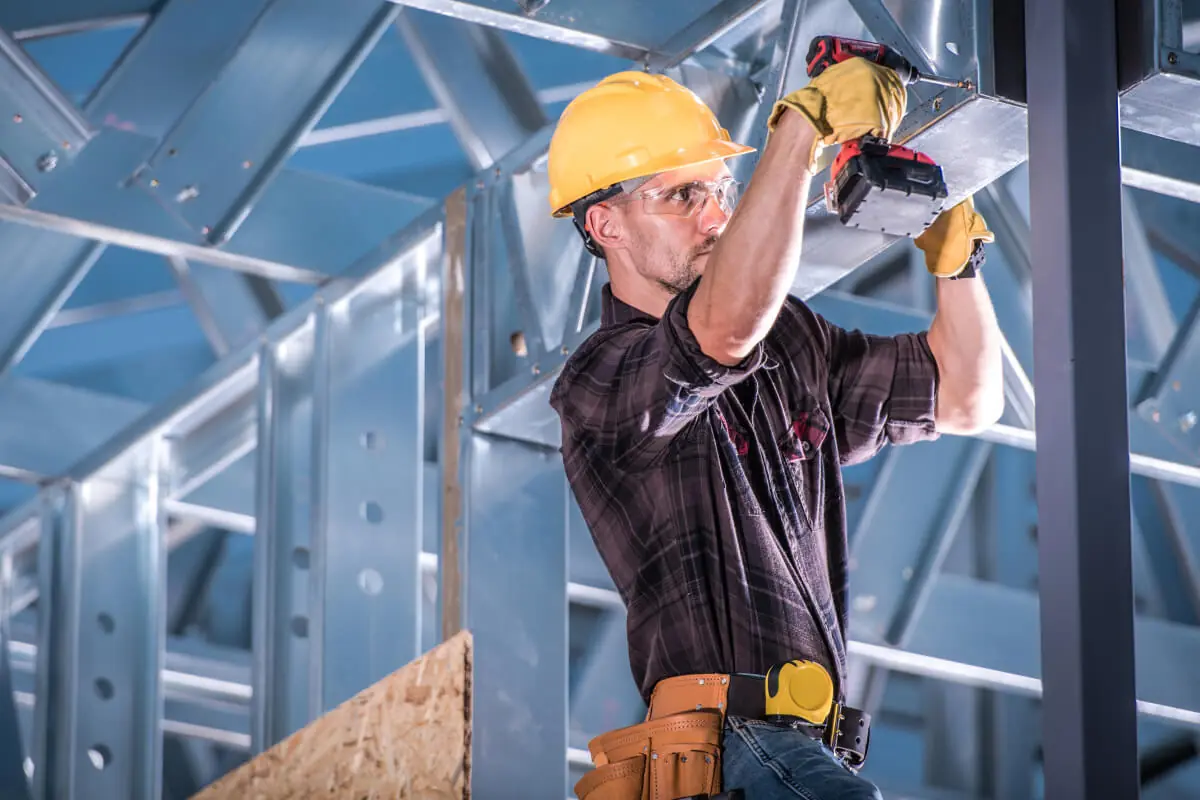
How to Choose the Right Construction Screws for Your Project
- Construction Screws
In building projects, even the smallest components can shape the final outcome. Construction screws are one such element. Chosen wisely, they ensure structural integrity, compliance with safety standards and building codes, as well as long-term durability. Chosen poorly, they risk structural deficiencies, increased costs and potential hazards. This article examines how to select the most appropriate construction screws, drawing on industry standards and expert advice.
Table of Contents
Understanding Construction Screws
What Are Construction Screws and Why They Matter
Construction screws are specialized fasteners designed to securely join materials in building projects. Unlike general-purpose screws, they are engineered to meet specific structural requirements and accommodate various materials such as wood, metal, and masonry. Their design considers factors like load-bearing capacity, environmental conditions, and compatibility with the materials used.
The significance of construction screws extends beyond mere assembly; they are pivotal to a building’s structural integrity. A well-chosen screw ensures that components are firmly connected, distributes loads effectively, and resists environmental stresses. This is particularly crucial in regions susceptible to extreme weather conditions, where structural resilience is essential.
A report by the National Institute of Standards and Technology (NIST) indicates that fastening failures account for up to 12% of structural deficiencies in residential buildings. This statistic underscores the critical role that proper screw selection plays in construction. Additionally, the International Code Council (ICC) states that adherence to building codes can reduce the risk of structural failure by up to 25%. These figures highlight the tangible impact of selecting appropriate fasteners.
Construction screw suppliers play an essential role in this context. They offer not only a variety of specialized screws but also the expertise needed to navigate the complexities of selection. A reputable supplier provides guidance on the most suitable products for specific applications and ensures compliance with industry standards and regulations. Partnering with knowledgeable suppliers enables builders to access quality materials that meet the stringent demands of modern construction.
Summary of Construction Screw Types and Materials
To provide a clear overview, here are tables that summarize the common types of construction screws and the materials/coatings used in their manufacture.
Key Factors in Choosing the Right Construction Screw
Selecting the appropriate construction screw is vital for the safety and longevity of any building project. Several factors influence this choice, ranging from the materials involved to environmental conditions and compliance with building codes. Below are the key considerations to guide you in making an informed decision.
1. Material Compatibility
Selecting a screw material that is compatible with the materials being joined is crucial to prevent chemical reactions and corrosion. In wood applications, using stainless steel or coated carbon steel screws is advisable. These materials resist corrosion caused by tannins and other compounds naturally present in wood, thereby enhancing the longevity and integrity of the connection.
In metal applications, it is recommended to use screws made from the same type of metal as the material being fastened. This practice avoids galvanic corrosion, a process that occurs when dissimilar metals come into electrical contact in the presence of an electrolyte (such as moisture), leading to accelerated deterioration of the metals involved.
For example, fastening aluminum panels with aluminum screws prevents the galvanic reaction that would occur if steel screws were used instead.
Understanding the suitability of different screw materials helps in making informed decisions:
- Carbon Steel Screws: Suitable for indoor wood projects due to their strength and cost-effectiveness.However, they are not recommended for outdoor or wet environments because they are prone to rust when exposed to moisture.
- Stainless Steel Screws: Ideal for outdoor and corrosive environments owing to their high resistance to rust and corrosion. They are particularly useful in projects exposed to weather, moisture, or chemicals. While stainless steel screws offer excellent corrosion resistance, they may not always be suitable for high-stress applications unless specifically designed for that purpose.
- Galvanized Steel Screws: These screws are coated with a layer of zinc to provide moderate corrosion resistance, making them appropriate for general outdoor use. Nevertheless, they are not suitable for marine environments, where the presence of salt can accelerate corrosion despite the galvanized coating.
- Brass Screws: Often used in decorative applications due to their attractive appearance and resistance to tarnishing. However, brass screws have lower strength compared to steel screws and are not recommended for structural connections that bear significant loads.
2. Environmental Conditions
The environment where the screw will be used significantly influences its performance and durability. For indoor projects not exposed to moisture or harsh conditions, standard carbon steel screws may be adequate. However, in outdoor settings or areas with high humidity, it’s essential to use screws that offer corrosion resistance. Stainless steel screws are ideal for outdoor and moisture-prone environments due to their excellent resistance to rust. Galvanized steel screws, coated with a layer of zinc, provide moderate corrosion resistance suitable for general outdoor use. In environments exposed to chemicals or saltwater—such as coastal areas—using screws with high corrosion resistance, like ceramic-coated or marine-grade stainless steel screws, helps prevent premature failure caused by corrosion. Selecting screws that match the environmental conditions ensures the longevity and integrity of the construction.
3. Load Requirements
Assessing the load requirements is crucial to ensure that the screws can handle the forces they’ll encounter without failing. Screws must possess adequate shear strength to resist forces that might cause them to slide sideways and sufficient tensile strength to withstand forces that attempt to pull them apart. Identifying the maximum load the screw will support allows you to choose a screw rated higher than the expected load, providing a safety margin. Manufacturer specifications often include load ratings, which should be consulted to select the appropriate screw. By matching the screw’s strength to the project’s demands, you help ensure structural integrity and prevent potential failures.
4. Coatings and Treatments
Coatings and surface treatments are essential for enhancing the durability and performance of construction screws. They provide protection against environmental factors like corrosion, thereby extending the lifespan of the fasteners. Below is a table summarizing common coatings and treatments used for construction screws.
Summary of Screw Coatings and Treatments
Brief Overview of Each Coating
- Galvanized Coating: Involves applying a layer of zinc to the screw, providing moderate resistance to corrosion. It’s suitable for general outdoor applications where exposure to moisture is expected but not extreme.
- Ceramic Coating: Offers high corrosion resistance, making it ideal for screws used in pressure-treated lumber and coastal areas where exposure to harsh elements is significant.
- Phosphate Coating: Enhances the screw’s ability to hold paint and provides minimal corrosion resistance. This coating is typically used for screws in indoor applications where aesthetics and paint adhesion are important.
Compliance with Building Codes
Adhering to local and international building codes is a fundamental aspect of selecting the appropriate construction screw. These codes are established to ensure the safety, structural integrity, and longevity of buildings. They provide specific guidelines on materials, fastener types, installation methods, and performance requirements that must be met to comply with legal and safety standards.
Using screws that meet or exceed these codes helps prevent structural failures and legal complications.
According to the International Code Council (ICC), adherence to building codes can reduce the risk of structural failure by up to 25%. This statistic underscores the significant impact that compliance has on the overall safety and performance of a building.
Role of Construction Screw Suppliers
Reputable construction screw suppliers play a crucial role in ensuring compliance:
- Expert Guidance: Suppliers can provide advice on selecting screws that meet specific code requirements for your project.
- Quality Assurance: They offer products that have been tested and certified according to industry standards, ensuring reliability and safety.
- Technical Support: Access to technical resources and customer support helps in understanding and applying building code requirements effectively.
As an expert supplier and manufacturer of a wide range of construction screws for global projects, Cheng Hao is ideally placed to help you make the right fastener choices for your construction projects. Please contact us to discover how we can help you.